What is Magnet Wire?
The term “magnet wire“ is used to describe solid conductor wire—usually copper—insulated with a polymer-based film. The films are designed to provide a uniform dielectric coating while taking up as little space as possible.
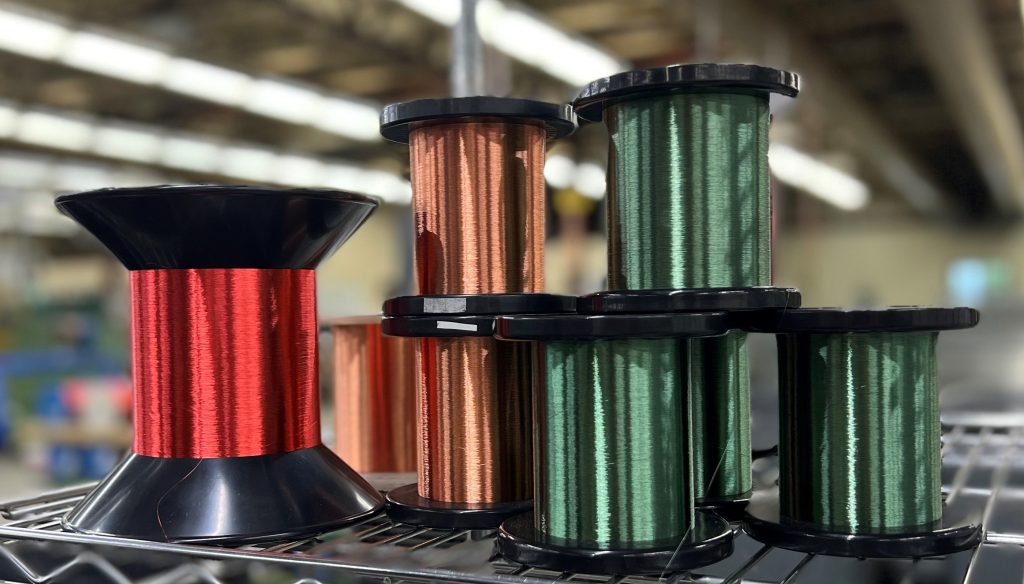
In specifying a magnet wire, there are several areas an engineer needs to be concerned with including:
- Size or Diameter
- Insulation Thermal Class
- Insulation Build or Thickness
- Color and Coatings
All the magnet wire used in manufacturing our Litz wire is certified to the most rigorous requirements of federal, NEMA and military specifications.
The chart below displays some commonly used magnet wire film insulations. Please note, this is not an exhaustive list and other options may be available for your project.
Insulation | Temperature Rating | AWG | Advantages | Considerations |
---|---|---|---|---|
Polyvinyl Formal | Class 105C MW 15-C | 14 - 50 | - Excellent abrasion resistance - Excellent compatibility with transformer oils - Good electrical proper ties - Used in Cryogenic Applications | - Must be stripped before soldering - Should be annealed before application of varnish |
Polyurethane | Class 155C MW 79-C Class 180C MW 83-C | 30 - 50 24-50 | - Excellent electrical properties for high "Q" coils - Easily solderable 390C/360C - Excellent film adhesion & flexibility - Good moisture & chemical resistance | - Not recommended for applications with the possibility of severe thermal overload |
Polyurethane-Nylon | Class 155C MW 80-C Class 180C MW 83-C | 10 - 46 25 - 46 | - Good electrical properties - Easily solderable 430C/390C - Excellent film adhesion & flexibility - Improved chemical & mechanical resistance from nylon topcoat - Nylon overcoat provides low coefficient of friction | - Not recommended for applications with the possibility of serve thermal overload - Nylon topcoat is hygroscopic |
Solderable Polyester | Class 180C MW 77-C | 14 - 50 | - Solderable 470C - Excellent thermal proper ties - Good electrical proper ties - Good compatibility with varnishes & solvents - Improved thermal overload - Good moisture resistance | - Low abrasion resistance compared to Nylon & amide imide topcoat materials - Preheat before varnishing is recommended |
Solderable Polyester Nylon | Class 180C MW 78-C | 14 - 50 | - Solderable 470C - Excellent thermal proper ties - Good electrical proper ties - Good compatibility with varnishes & solvents - Improved thermal overload - Good moisture resistance - Nylon overcoat provides low coefficient of friction | - Nylon topcoat is hygroscopic - Preheat before varnishing is recommended |
Polyester Amide-Imide | Class 200C MW 74-C | 34 - 44 | - Excellent flexibility & abrasion resistance - Excellent thermal overload - Excellent dielectric strength - Excellent moisture resistance - Good chemical resistance | - Must be stsripped before soldering - Not recommended for use in oil- filled transformers - Preheat before varnishing |
Polyester/Poly-amideimide | Class 200C MW 35-C | 8 - 33 | - Excellent flexibility & abrasion resistance - Excellent thermal overload - Excellent dielectric strength - Excellent moisture resistance - Good chemical resistance | - Must be stripped before soldering - Preheat before varnishing |
Polyimide | Class 240C MW 16-C | 10 - 30 | - Excellent flexibility - Excellent thermal overload - Excellent dielectric strength - Excellent moisture resistance - Excellent chemical resistance - High dielectric strength - Adequate abrasion resistance - Low outgas | - Must be stripped before soldering - Must be annealed before varnishing - Will solvent craze |