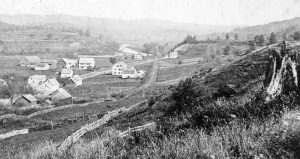
We have been a pioneer in Litz wire design and manufacture in the United States for decades. Take a stroll down memory lane with us…
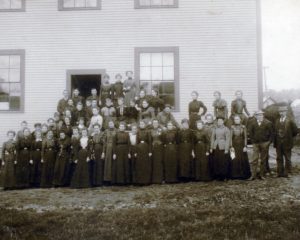
In Lisbon, New Hampshire, over 120 years ago at the dawn of the communication age, New England Wire (then known as New England Electrical Works) began manufacturing single and double silk wrapped copper wire (an early form of today’s film insulated magnet wire) for use in the manufacture of magnetic solenoid coils necessary to ring the bells in old-fashioned crank telephones.
Fun fact: Look at all the female employees in this photo from 1899! Women were preferred to men as early machine operators due to their smaller hands and better manually dexterity. In the early days, the average regular wage for these operators was $6/week
About 1912, enameled copper wire replaced the served or wrapped wire in many applications. It was during this time that New England Wire began making Litz wire, where multiple strands of the enameled wire were “woven” together to make a wire conductor. As a matter of fact, New England Wire was the first US manufacturer to make Litz wire on a commercial basis.
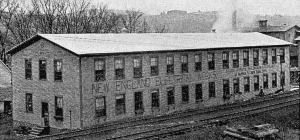
The name Litz comes from the German word “litzendraht” (litzen meaning braids, and draht meaning wire). Litz may be seen as a product bridging the electrical and electronic age. Its first principal commercial application was in radio coils. By its woven configuration of multiple insulated strands, the resistance to the flow of current at higher frequencies is greatly reduced as compared to a solid wire of similar cross-sectional area. This increase in efficiency made Litz the conductor of choice for many applications in the emerging radio industry.
Fun fact: the photo to the left is of the original building constructed in 1899. This building still stands today and is used mainly for office space and storage. A third floor was added in 1915.
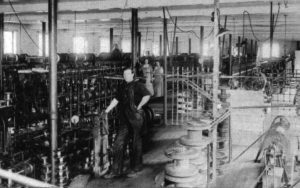
During the 1920’s and Depression era, Litz was a mainstay product for New England Wire where the textile-served enameled wire, continued to be in demand as frugal customers used it to rewind worn motors that had been manufactured decades earlier.
In the early 1940s New England Wire advertised custom work specializing in fine enameled copper wire used in Litz and processed with silk, rayon, nylon, spun glass or cotton, as required. World War II was, for its time, a “high tech” war with radar and weaponry reliant on fine instrumentation. New England Wire supplied the defense effort with Litz wire, aircraft antenna wire, braided metal shielding, mercury switch wire, and dozens of other products.
As the Space Age and medical electronics progressed, miniaturization became the password of the electronic industry. New England saw a growing need for ultra-flexible microminiature insulated cables. Practically speaking, there were no other cable manufacturers in this segment of the market. The techniques for stranding ultra-fine conductors composed of wires as fine as 1/1000 of an inch had already been developed by New England Wire, and so the company had a head start on others in the wire industry. New England was able to obtain equipment and further refined it to provide the capability of applying insulations of Teflon®, PVC, polyethylene and nylon in wall thickness as thin as 3/1000 of an inch. Success in this area was outstanding and enabled the company to meet the constantly changing and critically precise tolerances of the electronic applications of the time.
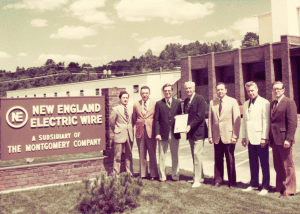
In 1963, the company name was changed to New England Electric Wire. During the latter part of 1968 and through 1969 New England had been approached by Continental Electronics in Dallas and The Naval Electronics Laboratory in San Diego to help design and manufacture two large Litz cables for the new Omega Radionavigation System. The Omega Radionavigation System consisted of eight large Very Low Frequency (VLF) radio transmitters spaced around the world. By receiving signals from three stations, an Omega receiver could locate a ship or aircraft’s position to within four miles. At the time, this accuracy was considered quite acceptable. New England Wire made cables for both the transmitter’s Helix and Variometer windings.
To better reflect the diversity and sophistication of product offerings, in 1996 the company name was changed once again to New England Wire Technologies, as it is known today. Currently, the facilities consist of over 385,000 square feet of manufacturing, quality/testing, tooling/machine fabrication, and office space, and we employee more than 400 employees operating three shifts, five days a week.
Since pioneering the manufacturing of Litz wire in 1912, New England has designed and manufactured thousands of different constructions for use over the E.L.F. through H.F. frequency ranges. Today we manufacture custom Litz designs for high frequency inductors and transformers, inverters, converters, high Q circuitry, linear induction and permanent magnet motors, induction heating coils, specialty audio, and wireless power transfer. Our Litz wire is a critical component in these applications – working to improve surgical robotics, paving the way for efficient battery-powered vehicles, supporting alternative energy generation, and being a key supplier for state-of-the-art military applications. We are most proud of our decades long legacy of manufacturing 100% of our custom wire and cable products right here in Lisbon, NH, USA with our highly skilled and dedicated work force.
We can’t wait to see what the future holds.
To learn more about our full array of products and capabilities beyond custom Litz wire, visit us at newenglandwire.com